The construction industry has always been at the forefront of innovation, constantly looking for new methods and technologies to improve efficiency, reduce costs, and enhance sustainability.
In recent years, modular construction has emerged as a game-changer in the building industry.
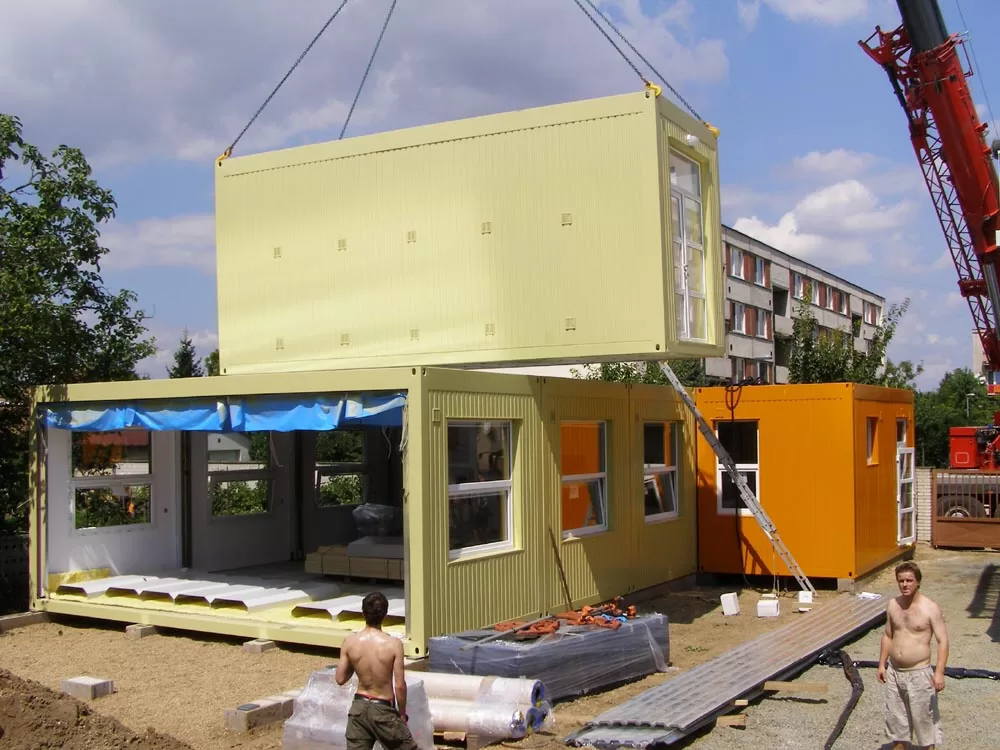
This revolutionary approach involves the off-site manufacturing of building supplies and components, sometimes known as modules, which are then transported to the construction site for assembly.
In this blog post, we will explore the concept of modular construction and highlight its remarkable benefits.
Understanding Modular Construction
Modular construction, also referred to as prefabricated or off-site construction, is a process where building components are manufactured in a controlled factory environment and later assembled on-site.
modules are constructed with precision and adhere to strict quality standards. They can be customized to suit the specific requirements of each project, whether it’s residential, commercial, or institutional construction.
Read Also:
Accelerated Construction Timeline
One advantage of modular construction is its ability to significantly reduce project timelines. Unlike traditional construction methods, where multiple tasks are performed sequentially on-site, modular construction allows for parallel work processes.
While modules are being fabricated in the factory, site preparation can progress simultaneously.
This parallel workflow results in a streamlined construction process, reducing the overall project duration by up to 50%. Consequently, clients can enjoy faster project completion and earlier occupancy of their buildings.
Cost Efficiency
Modular construction offers substantial cost savings compared to conventional construction methods. The controlled factory environment minimizes material waste and optimizes the use of resources, leading to reduced material costs.
The precise manufacturing process ensures efficient use of materials and eliminates the need for excess on-site storage. Moreover, the assembly of prefabricated modules requires less on-site labor, resulting in decreased labor expenses.
With reduced construction time and optimized resource allocation, modular construction proves to be a cost-effective solution for a wide range of building projects.
Enhanced Quality Control
The factory-controlled environment of modular construction plays a crucial role in ensuring consistent quality throughout the building process.
The modules are manufactured using standardized procedures, eliminating variations and errors commonly encountered on traditional construction sites. Quality control measures, such as strict inspections and adherence to industry standards, are implemented at each stage of production.
Additionally, the protection offered by the factory environment mitigates the risk of material damage due to weather conditions. The result is a higher level of quality assurance and a finished product that meets or exceeds industry standards.
Sustainable Construction
In an era where environmental consciousness is paramount, modular construction stands out as an eco-friendly building method. The controlled factory environment facilitates efficient waste management, as excess materials can be recycled or reused.
The optimized use of resources, including energy and water, reduces the overall environmental impact of the construction process. Additionally, the ability to transport modules to the construction site reduces the need for the transportation of raw materials, minimizing carbon emissions and traffic congestion.
With its focus on sustainability, modular construction aligns with the global push for greener building practices.
Design Flexibility and Adaptability
Modular construction offers tremendous design flexibility and adaptability. The modules can be customized to suit specific architectural designs and functional requirements. They can easily be reconfigured or expanded to accommodate future changes or additions.
This adaptability is particularly advantageous for sectors such as healthcare and education, where buildings need to evolve to meet shifting needs over time.
The modular approach allows for efficient modifications and upgrades, ensuring that the structure remains functional and relevant for years to come.
Improved Safety Measures
Worker safety is a top priority in the construction industry. Modular construction significantly reduces on-site risks as a large portion of the construction process is moved to a controlled factory environment.
This minimizes hazards associated with adverse weather conditions, working at height, and potential on-site accidents. The factory setting provides a safer working environment with enhanced safety protocols, minimizing the risk to construction personnel.
The focus on safety in modular construction contributes to a healthier and more secure construction process.
Unlocking Modular Construction: Advantages and Benefits
Modular construction, also known as prefabricated or off-site construction, offers a wide range of benefits that are transforming the building industry. Here are some key advantages of unlocking modular construction:
Speed of Construction
Modular construction significantly reduces project timelines compared to traditional construction methods. By fabricating building components off-site simultaneously with site preparation, the overall construction process is streamlined.
This parallel workflow allows a project to be completed, enabling clients to occupy their buildings sooner and reducing the overall construction timeline by up to 50%.
Cost Efficiency
Modular construction presents a cost-effective solution for developers and clients. The controlled factory environment minimizes material waste and optimizes the use of resources, leading to reduced material costs.
The efficient manufacturing process also reduces labor expenses as the assembly of prefabricated modules requires fewer on-site workers. Additionally, the shortened construction timeline results in cost savings associated with labor, financing, and overhead expenses.
Quality Control
Modular construction ensures a higher level of quality control compared to traditional construction methods.
The manufacturing process takes place in a controlled environment, allowing for standardized production procedures and stringent quality inspections at each stage.
The precise engineering and attention to detail result in consistently high-quality modules that meet or exceed industry standards.
The controlled environment also protects materials from weather-related damage, ensuring long-term durability.
Design Flexibility
Modular construction offers design flexibility and customization options. The modules can be tailored to meet specific architectural and functional requirements, allowing for unique designs and customization.
From residential homes to commercial buildings, modular construction can accommodate a wide range of design styles and purposes. The ability to customize and adapt modules makes it easier to meet the specific needs of different projects and clients.
Sustainability
Modular construction aligns with sustainable building practices and environmental consciousness. The controlled factory environment allows for efficient waste management, with excess materials being recycled or reused.
Resource optimization, including energy and water usage, is optimized in the manufacturing process, reducing the overall environmental impact.
Moreover, the ability to transport modules to the construction site minimizes the need for the transportation of raw materials, reducing carbon emissions and traffic congestion.
Enhanced Safety
Safety is a top priority in any construction project, and modular construction prioritizes worker safety. By shifting a significant portion of the construction process to the factory setting, on-site risks are reduced.
Workers are safer with fewer hazards associated with adverse weather conditions, working at heights, and potential on-site accidents. The factory environment allows for enhanced safety protocols, ensuring a safer working environment for construction personnel.
Adaptability and Future-proofing
Modular construction offers adaptability and future-proofing for buildings. The modular units can be easily reconfigured, expanded, or repurposed to accommodate changes in design or functionality.
This flexibility is particularly advantageous in sectors such as healthcare and education, where buildings need to change needs over time.
With modular construction, modifications, and upgrades can be efficiently implemented, ensuring that the building remains functional and relevant for years to come.
Modular construction has completely changed the building industry, offering many different benefits that revolutionize the way structures are designed and built.
The accelerated construction timeline, cost efficiency, enhanced quality control, sustainability, design flexibility, and improved safety measures make modular construction an attractive choice for developers and clients alike.
As the world continues to prioritize speed, cost savings, environmental responsibility, and adaptability, modular construction is unlocking a new era of construction that is efficient, sustainable, and future-proof.
By embracing modular construction, we are building a better, smarter, and more sustainable future for the construction industry.