MIG welding is one of the most common welding techniques and with a good reason since it’s the fastest and cheapest method to join two large pieces made of thick materials.
In addition to that, it’s also one of the easiest to learn and master, which makes it suitable not only for industry professionals but also for newbies.
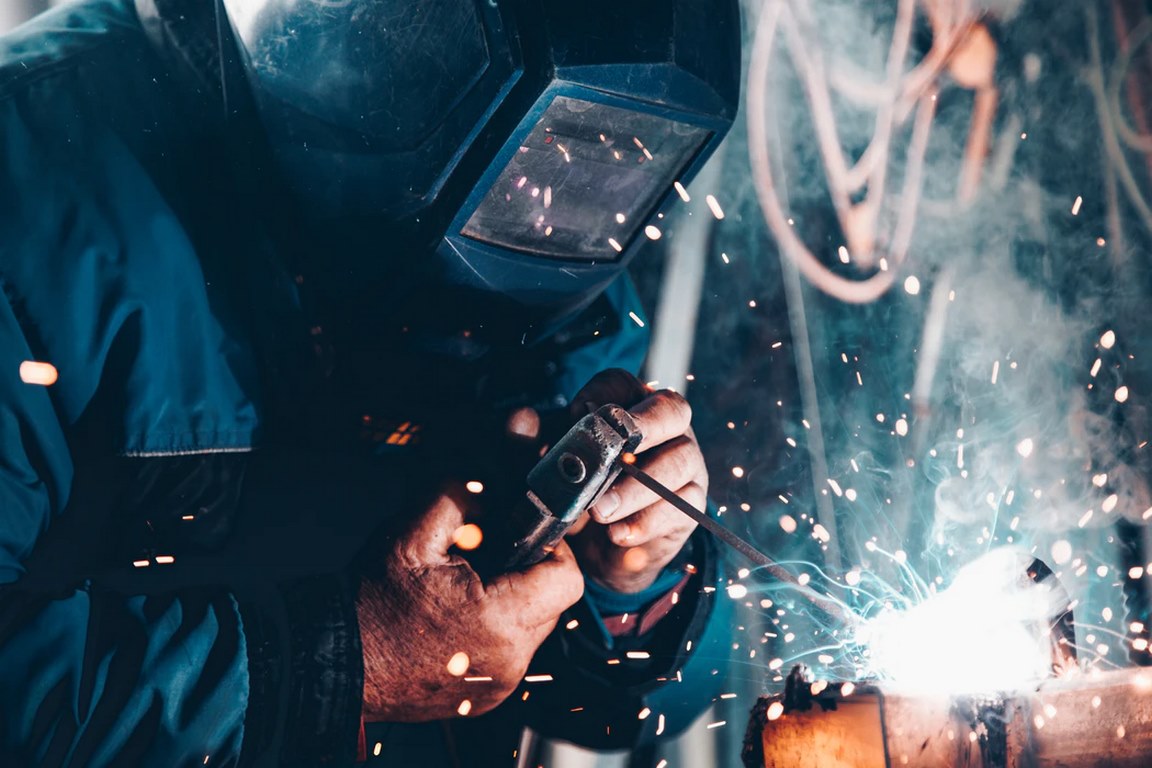
However, that doesn’t mean a beginner can just get at it without being well-prepared and equipped with a certain knowledge of the entire process.
If you are one of the newly-minted welders plotting to bring to life their own project, read on to dive into the nitty-gritty of this popular welding technique.
What Is MIG Welding?
Let’s start with a brief definition of MIG, which is, actually, a type of arc welding process that serves the only purpose – to join two metals.
As you have probably already guessed, those metals are heated with the help of an arc, hence the name.
To put it simply, the MIG Welding process utilizes a wire that plays the roles of both electrode and filler material.
Shielding gas is employed for the protection of the molten pool of weld metal in order to avoid reactions with various compounds present in the atmosphere.
Needless to say, this method requires Reverse Polarity or a DCEP, which is short for Direct Current Positive Electrode.
Basic Terms You Need to Know
Parent metal – the metal you are going to join by welding.
Filler Metal – the metal you add throughout the process in order to join the metals together.
Weld Metal – this term covers all the metal you’ve melted and retained during the creation of the weld.
Heat Affected Zone – the piece of the parent metal that doesn’t melt even though it’s been affected metallurgically during the welding process.
Fusion Line – the border between the heat-affected zone and the weld metal. Keep in mind that it is not a standard term but it’s widely used to describe the weld junction.
Weld Zone – the area that consists of the heat-affected zone and the weld metal.
Read Also:
Welding Gun & Its Benefits
A welding gun is a name for a portable device used to form semi-automatic or automatic welds on pieces of metal.
Hooked up to a welding machine (or other power supply), it works with a wire feed, which, in its turn, can be cored or solid.
Apart from higher efficiency, the use of welding guns also brings a better quality of the created welds, significantly increased arc-on times, and as a result, greater productivity.
They are also convenient to use since the majority of welding guns have nozzles and tips that can be easily taken off to be cleaned or changed.
Which Metals Can Be MIG-Welded?
Almost all you have at your disposal. Well, of course, there are exceptions but don’t forget that one of the main reasons why this type of welding is so popular is nothing but its great ability to weld virtually any metal.
Plus, as already mentioned, this method is also cost-effective and incredibly fast. So, what metals exactly can be MIG-welded? Stainless steel, then carbon steel, aluminum, magnesium, copper, nickel, silicon bronze, and other alloys.
By the way, carbon steel is considered the easiest one to MIG weld.
Metal Transfer Modes
The metal can be transferred from the wire electrode to the weld pool in four different modes, each has its own purpose and specificities.
Let’s take a closer look at all of them for a better understanding of the process.
Short-Circuiting Mode
Being a low-heat method of metal transfer, the short-circuiting mode is known for its all-position capability and incredible ability to deal with poor fit-up, which altogether makes it a great option for pipe applications.
Due to low heat, it also provides for reduced weld distortion while the electrode efficiency often reaches an impressive 93%. The ease of use does add to the overall picture.
Globular Mode
This method comes with a plethora of benefits but the major one is perhaps its ability to produce welds at lightning speed.
In addition to that, it is a great money-saver given the use of carbon dioxide as a shielding gas, as well as leveraging advantages of metal-cored or solid electrodes, which are also really inexpensive.
The specificity of globular mode is that the electrode doesn’t come in contact with the base material.
Spray Mode
A high-energy mode that delivers a great electrode efficiency of up to 98%, this method is compatible with a broad range of fillers.
In contrast to the globular counterpart, the spray mode facilitates a consistent stream of small droplets of molten metal, producing an almost perfect look of the weld bead.
It is also easily adaptable to hard-automation, robotic, as well as semi-automatic applications.
Pulsed Mode
This method is actually a variant of the spray mode that provides for a highly controlled transfer of metal.
According to the great bulk of seasoned welders, the pulse mode is arguably the most advantageous of all methods and delivers the best results.
The weld beads look really stunning while the electrode efficiency hits an impressive 98%.
Applications
As already said, metal inert gas welding is one of the most commonly used methods for joining metals, hence it’s widely applied across different industries.
For instance, MIG is the most popular type of welding within the huge automotive industry, which is no wonder providing that it delivers strong and robust welds.
Besides being irreplaceable for all kinds of repairs needed for vehicles of all sizes and models, this type of welding is also used in pipe welds and sheet metal welding.
By and large, it’s safe to say, it is a great choice for lower-volume welding inside a metal workshop or a factory.
Metal inert gas (MIG) welding is the first choice for many manufacturing industries for many reasons but the fast creation of top-notch welds is certainly the main advantage of this technique.
It also requires minimum skills, which makes it suitable for newbies who are looking for a relatively uncomplicated and cost-efficient way to get high-quality welds.