Floor screeds are indispensable when it comes to forming a strong, level base for a flooring system. Choosing the right screed material is crucial in ensuring that flooring is long-lasting and provides high performance. There are a variety of materials to choose from: sand and cement-based, anhydrite, and polymer-based options are all available.
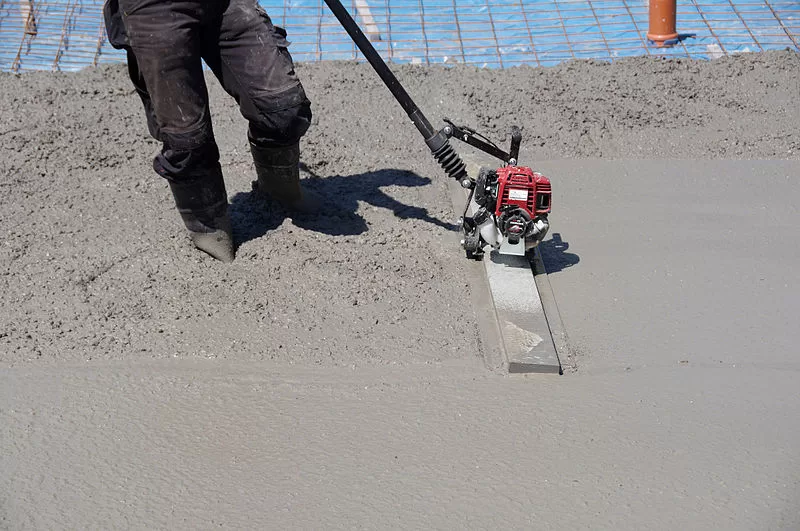
Deciding between the many options can be a complex process but with this in mind, this article sets out a comprehensive comparative analysis of floor screed materials – detailing their strengths, their weaknesses, and best applications.
Overview of different floor screed materials
Sand and cement
Composition and properties
Sand and cement floor screeds typically consist of a mixture of sharp sand, cement, and water. The ratio of sand to cement can vary, depending on the required strength and the screed depth. It is a traditional screed that remains extremely popular because of its excellent compressive strength and durability, making it suitable for use in a wide range of applications.
Installation process
The installation process by experts involves hand mixing the sand and cement in the required proportions, combined with water, to create a workable consistency. The screed is then poured onto the prepared substrate. The surface is then leveled using a straight edge or screeding bar, and a floating trowel is then used in a circular motion to smooth any trowel lines or marks. The screed should be allowed to cure sufficiently, and it can be finished accordingly.
Anhydrite
Composition and properties
Anhydrite floor screed comprises calcium sulfate binder, sand, and water. Anhydrite screed is a free-flowing, self-leveling screed known to be an exceptional thermal conductor, making it the ideal match for underfloor heating systems. Anhydrite screed can also dry much faster than conventional sand and cement screed.
Installation process
Anhydrite screed is typically poured over the substrate and left to self-level. It is important to start with a clean and primed substrate that promotes adhesion. Once laid, the screed is often finished using a final smoothing or power float.
Polymer-based
Composition and properties
Polymer-based floor screed consists of a conventional screed mix. Still, it utilizes synthetic resins or polymers added to the screed mix to enhance certain properties such as flexibility, durability, and chemical resistance. Depending on the product used, these chemical resins or polymers can be added at the initial mixing stage or as a powder additive to suit site conditions and performance requirements. This makes these types of modified screeds suitable for various applications, including industrial and commercial settings.
Installation process
The installation process is the same as that of a conventional screed. Polymeric screeds are mixed with water to create a workable consistency and applied directly to your substrate by hand, then using some means of straight edge or rule to level your floors. Curing and additional surface treatments may also be required again, depending on which product is specified.
Comparison of strengths and weaknesses of different floor screeds
Durability
- Sand and cement screed provides good compressive strength, making it a strong choice for heavy-duty applications.
- Anhydrite screed offers comparable durability with the added benefit of being well-suited to use with underfloor heating systems.
- Polymer-based screeds can offer greater durability and impact resistance, making them a popular choice for industrial environments.
Flexibility
- Polymer-based screeds typically offer enhanced flexibility compared to traditional screeds. This can help to reduce the risk of cracks developing in the finished surface.
- Some flexibility is also a desirable trait of anhydrite screeds, mainly when they are used in conjunction with underfloor heating systems.
- Although sand and cement screeds can be highly durable, they are often less flexible and may be prone to cracking in the wrong conditions.
Drying time
- Anhydrite screed usually boasts a quicker drying time than sand and cement screed, making it a good solution for projects where time is precious.
- Drying times for polymer-based screeds can vary depending on the specific product being used and the environmental conditions during installation.
- Sand and cement screeds tend to have the longest drying times out of the options listed here.
Best applications for each type of floor screed
Sand and cement screed is generally used in residential and light commercial areas due to its good compressive strength and general use.
Anhydrite screed is primarily used in projects with underfloor heating and for large areas where it can be beneficial to have faster drying times available.
Polymer-based screeds are used in industrial and heavy traffic areas due to their high durability and chemical resistance.
Each type of floor screeds’ properties are ideal for different buildings and applications and therefore will offer the best long-term performance in these areas.
Factors to consider when selecting a suitable floor screed
Project requirements
When selecting a floor screed, it’s important to consider the intended use of the space. Will the space be used for residential, commercial, or industrial purposes? Because the amount and intensity of foot traffic can vary, it’s also essential to evaluate load-bearing requirements to determine the screed’s required strength and durability.
Environmental conditions
Conditions in and around the project site may require specific screed properties. For example, factors such as temperature, humidity, or exposure to water and moisture can influence screed selection. It’s also important to choose materials with the appropriate resistance to substances like chemicals or organic matter present in the environment.
Budget constraints
Screeding a floor can be costly and time-consuming, so comparing these costs is important when selecting a floor screed. This should include the costs of materials, labor, and equipment and any long-term implications associated with the chosen screed, such as maintenance and repair.
Time constraints
In new construction, the drying time of the screed can be particularly important. Consideration must be given to project deadlines, and sometimes, it is worth paying a premium to ensure the screed delivers a rapid construction and drying time.
Final thoughts
In conclusion, selecting the right floor screed is paramount for ensuring the longevity and performance of flooring systems. By weighing project requirements, environmental conditions, budget constraints, time limitations, and long-term maintenance considerations, you can make an informed decision tailored to your specific needs, optimizing project outcomes.