There are many welding processes used today to perform tasks that were once done with hammers, or even the handheld pliers of yesterday.
The combination of power and precision has made this possible. You see, a good quality home welder will be the best tool for the job you need it to do. It is not a piece of technology, but a mix of technology, tools, and talent to put together a solution that will weld and make your project possible.
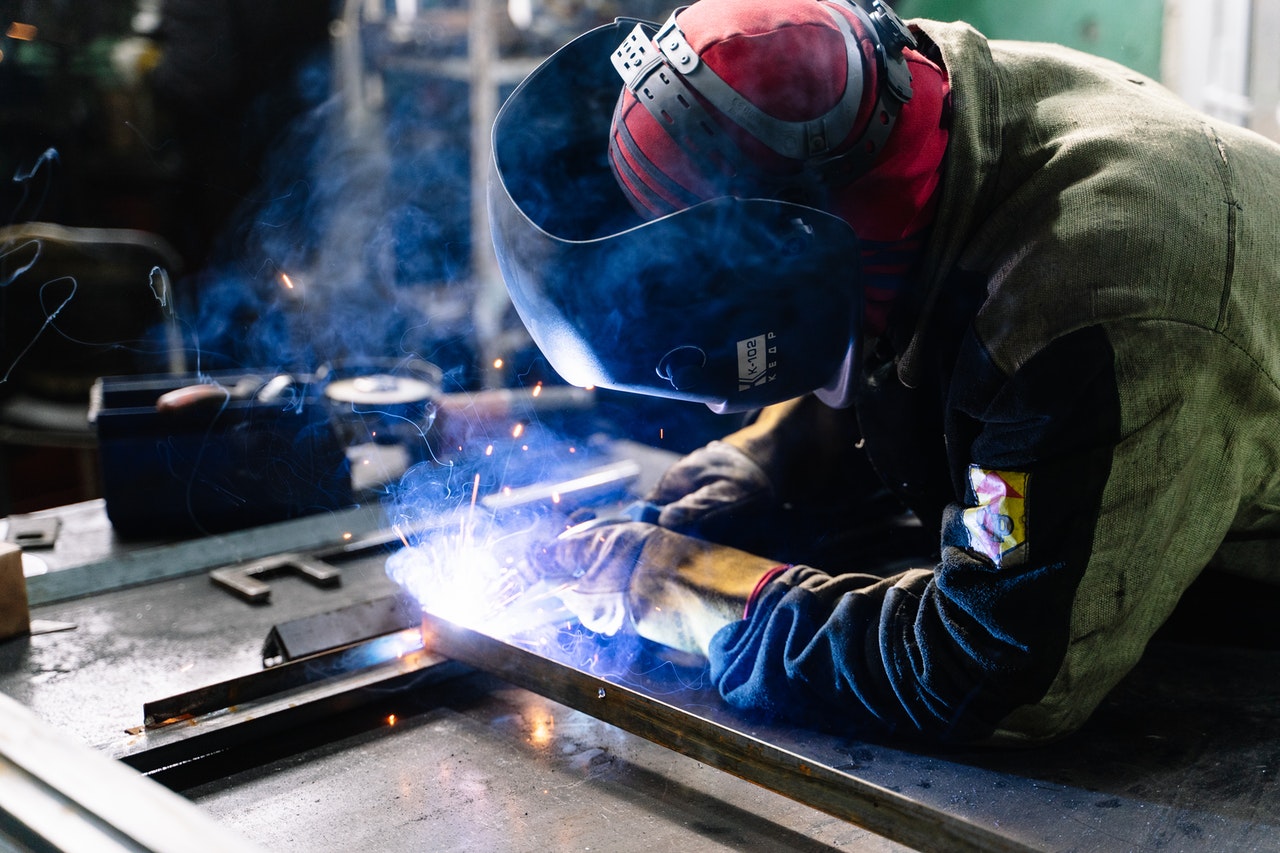
There are many things we are learning about the current technologies in welding processes, and the ones we use today are going to become obsolete before the year 2030.
Technology marches on, so do the welders, welder’s, and fabrication shops. They move along with the technology and there is no stopping them, they are going to continue to increase performance at a rate that surpasses what we thought was possible just a few years ago.
Besides, you can find some of the best welding machines for beginners out there at these two very well-known online shops.
Many people get caught up in the hype of the newest and greatest product on the market today and they tend to overlook the ones that have proven to be very efficient, cost-effective, and efficient tools.
Welding has proven to be one of the most successful products from the innovation process, as it has grown to be one of the largest industries today. To serve your welding, contractors, manufacturing industry, gshields.com has all types of essential industrial supplies for your project.
It is a specialized field of manufacturing, and the people who work with the welding machines understand all the facets of what it takes to do this job.
To become a welder in this industry, you will need to gain a lot of hands-on experience, and those welding courses that will allow you to see it up close and personal.
There are plenty of welder courses, but only some of them are going to offer you what you want. You will also need to be equipped with the knowledge and the tools needed to learn to weld.
Applying Safety Gear for MIG Welding
The first thing you need to do before you even start your project is to find out what equipment you will be using for your MIG welding work.
You will want to make sure that your welding equipment meets the requirements set forth by the local regulatory board or that you can acquire the equipment necessary from the location you are welding in.
If your welding equipment does not meet the local regulations, it is very important that you obtain a work permit to do any welding in the area. It is also very important that you obtain all of the equipment necessary before starting the work.
Another important aspect of planning your work is choosing a spot to weld. Most people who work with MIG welding use a variety of equipment depending on their experience level and where they will be welding.
You must find a place that has the proper welding tools and protective gear to protect yourself as well as others. There are two types of safety gear to protect you during work. The first is work gloves and the second is goggles.
MIG welding can be done with an arc lamp that has a cathode, an anode, and an anode being connected through a cathode hook-up.
This is one way to do MIG welding but if you want to learn the proper method of doing MIG welding, you will need to find a reputable professional to do the welding for you.
Since MIG welding requires special welding equipment, and since the cost of this equipment is so high, you must hire a skilled professional to do your work. You will also need to seek a way to pay for the expert’s services.
MIG welding equipment is very expensive, so you will want to do your homework before deciding to hire a professional for your MIG welding needs.
TIG Welding Is the Best Way to Keep Your Ductwork Cost-Effective
Using TIG welding to weld in ductwork is a great way to save money. There are two main types of ductwork, the solid surface, and the rolling surfaces.
The rolls are more flexible, but for the most part, they are thicker than the solid surfaces and therefore require TIG welding to get it into place. If you are looking to save on ductwork then this is the type of welding you want to use.
You can also use it in whatever the layout is. It is also much easier to do in this application.
Another great benefit is that this process does cost savings as well. If you are going to have ductwork made for ductwork purposes, you will be paying a high cost to have it made with a solid metal surface.
TIG welding is much cheaper than any other ductwork product. The low cost is one reason why it is used so often. The other reason is that since the roll is thinner, it requires less welding and therefore saves money by not having to have as many welds on it.
Ductwork can cost you quite a bit of money when you need it. It is essential to make sure that you save as much money as possible by using TIG welding for the work you need to be done on the roll.
Whether you have rolling surfaces or solid surfaces, TIG welding is the way to go to save money and get the ductwork designed to your specifications.
Using Flux Welding Equipment
Flux welding is the process of joining metal parts with a flux that is a very hot material. The hot flux is bonded to the part by gluing it in a certain place.
The part is then slowly heated up to its melting point before the welding can be done. A flux rod is inserted into the joint, which has already been welded.
Welding involves heating the entire part to a certain temperature which causes the flux to melt and causes the metal to bond with the flux and form a strong bond.
This type of welding equipment needs to be maintained very well to keep it in proper working condition. To keep the flux rods in good shape they need to be cleaned every few months or every so often.
The parts need to be kept away from oxygen, smoke, water, or chemicals because these may create problems with the material.
Rust also causes oxidation problems that can shorten the life of the part. Keep in mind that you do not need to clean the flux in between welds but you need to clean it every few months.