Plastic injection molding is a highly popular manufacturing process that is used extensively in the production of plastic products.
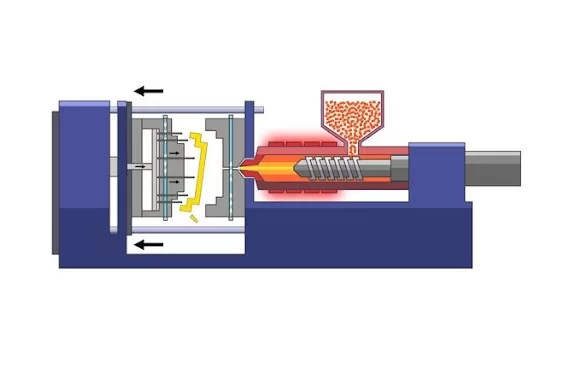
In this process, molten plastic is injected into a mold under high pressure, where it solidifies and takes the shape of the mold. This process is highly efficient and allows for the mass production of plastic products with consistent quality and accuracy. In this article, we will discuss the process of plastic injection molding and its applications in the B2B industry, including the production of different types of buckets.
The process of plastic injection molding begins with the creation of a mold. This mold is created using a highly precise CNC machine that cuts the mold into the desired shape. Once the mold is complete, it is placed into an injection molding machine, which is equipped with a hopper that holds the plastic pellets.
These pellets are melted and injected into the mold at high pressure, where they fill the mold and take its shape. Once the plastic has cooled and solidified, the mold is opened, and the finished product is removed. Plastic injection molding is widely used in the B2B industry, where it is used to produce a wide range of products, including automotive parts, medical devices, and consumer goods. One of the most popular applications of plastic injection molding in the B2B industry is the production of buckets.
Buckets are used extensively in the B2B industry for a wide range of applications, including storage, transportation, and packaging. There are several types of buckets that are commonly produced using plastic injection molding, including food-grade buckets, industrial buckets, and specialty buckets.
Food-grade buckets are used extensively in the food and beverage industry, where they are used to store and transport food products. These buckets are made using high-quality, food-grade plastic that is safe for use with food products. Food-grade buckets are available in a wide range of sizes and shapes, and they can be customized to meet the specific needs of the food and beverage industry.
Industrial buckets are used in a wide range of industrial applications, including the storage and transportation of chemicals, oils, and other hazardous materials. These buckets are made using high-quality, durable plastic that is resistant to chemical corrosion and other forms of damage. Industrial buckets are available in a wide range of sizes and shapes, and they can be customized to meet the specific needs of the industrial sector.
Specialty buckets are used in a wide range of specialized applications, including the storage and transportation of sensitive electronic equipment, medical supplies, and other high-value products. These buckets are made using specialized plastics that are designed to provide the required level of protection for the products they are used to store and transport.
Plastic injection molding is a highly efficient and cost-effective manufacturing process that is widely used in the B2B industry. It allows for the mass production of high-quality plastic products with consistent quality and accuracy, making it ideal for the production of buckets and other plastic products. By using plastic injection molding to produce buckets, B2B businesses can take advantage of the many benefits of this process, including lower production costs, faster production times, and greater flexibility in design and customization.
In Conclusion
Plastic injection molding is a highly effective and versatile manufacturing process that is widely used in the B2B industry. By using this process to produce buckets, B2B businesses can take advantage of the many benefits of plastic injection molding, including lower production costs, faster production times, and greater flexibility in design and customization.
Whether they are producing food-grade buckets, industrial buckets, or specialty buckets, B2B businesses can rely on plastic injection molding to deliver high-quality, durable, and cost-effective products that meet their specific needs and requirements.